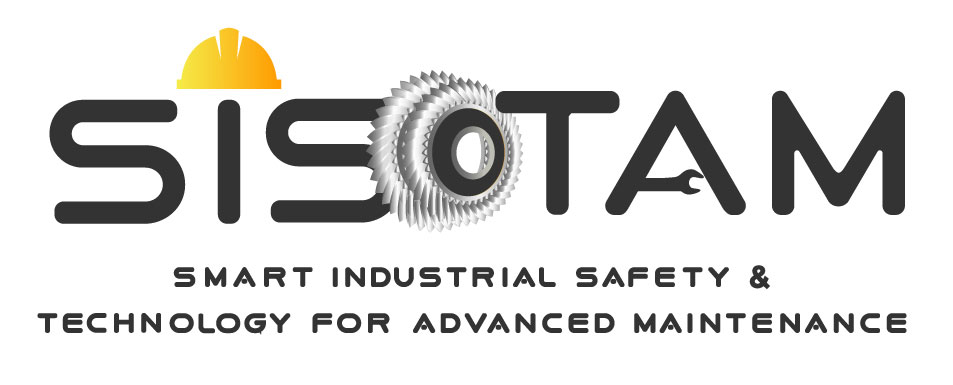
The best safety precaution is to prevent activities that are hazardous whether it is immediate injury or long-term ailments. A collaborative robot is a workplace innovation that allows employees to minimize their effort in high-risk lifting activities and other material handling activities. Robots aid employees by doing heavier or more risky lifts. This prevents back injuries and other types of accidents. It also avoids the presence of humans in hazardous areas with dust, chemical, and extreme heat. Apart from manufacturing and warehouse applications the cobots are beneficial to healthcare environments to lift patients or for movements in hotels. The workplace safety trend thus reduces ergonomic hazards by decreasing repetitive tasks.
Even when sensors and detectors are in place certain workplaces require visual inspection to ensure assets are operating within the safety codes. In facilities like oil and gas plants, power plants, construction sites, mines, and utility grids the functional parameters captured by sensors do not paint the complete picture. Visual inspection of huge storage tanks, transmission lines and other infrastructure expose workers to the risk of fall and other injuries. Here remotely controlled or autonomous drones and unmanned aerial vehicles (UAV) provide these workplaces with a safer alternative. Drones mounted with cameras and other essential equipment collect safety critical metrics accurately, removing the possibility of human error. This workplace safety trend also includes drone innovations that improve flight maneuverability allowing the inspection of difficult-to-reach locations.
The monitoring of workplace safety in a vast workplace like a factory or a mine is a challenge. Even in a small workplace like an office manual monitoring of hazardous conditions is not the ideal solution. IIoT innovations have led to solutions like smart sensors and devices that are capable of continuously monitoring their surroundings and infrastructure. These devices include hazardous material sensors that assess the levels of toxic gases, and equipment monitoring devices that capture various machine parameters that indicate the equipment’s condition. This workplace safety trend provides real-time data that allows safety engineers and managers to rapidly identify any issues that might lead to a potential hazard.
Every accident is the result of a chain of events, culminating in damage to infrastructure, injury, or even death. With the digitalization of workplaces, organizations have access to a multitude of data that is able to represent the state of a work environment at each moment. This data includes environment sensor data, employee logs, equipment sensor data, and even surveillance images. Developments in AI provide solutions that derive insights from these data sets that improve the safety of workplaces. These solutions use machine learning (ML) algorithms on historical data to recognize patterns that serve as a reference to detect anomalies that might lead to accidents. The workplace safety trend thus facilitates the early identification of safety threats and also predicts catastrophic failures, allowing maintenance managers to take proactive actions like preventive maintenance.
Autonomous vehicles, or self-driving cars, are designed with sensors and software to follow road contours, to avoid other vehicles, objects, bikers, and pedestrians, to adjust to unsafe weather conditions, to anticipate dangers from situations that are developing on the road ahead.
For the transportation industry and other fields that rely on vehicles to transport products or employees, it’s believed that large-scale AV deployment will significantly lower vehicle accident rates and fatalities. And, AVs have the potential to greatly reduce fuel and labor costs.
Safety instructions and training activities involve the sharing of knowledge that guides employees on how to proceed safely through their daily activities. A theoretical explanation of do’s and don’ts stand the risk of omissions and commissions due to a lack of practical understanding. Immersive technologies like virtual reality (VR) and augmented reality (AR) provide organizations with a visualization tool that drastically improves the effectiveness of safety training. A fully immersive experience helps the employee to understand the intent of each precautionary action. This facilitates a change in the mindset of employees, perceiving safety regulations as essential to their personal safety rather than a mandate forced up by the organization. AR technologies also allow the embedding of safety warnings and instructions in the workplace, which simplifies collaborative work and personnel changes. This workplace safety trend in this way improves employee vigilance and avoids resistance to accepting new safety regulations.
Communication is very important in the efficient operation of a safety management system. Traditional practices involving paper and spreadsheets lead to repetitive and mundane tasks even for the reporting of a minor safety incident. Moreover, the lack of a live self-updating dashboard might overlook certain data that is impossible to salvage from the manually entered documents. Digital innovations driven by new cloud computing and API development techniques led to the introduction of safety reporting software that automates safety management tasks. Web-based software and mobile apps aid in work permit management, incident management, safety compliance, employee risk management, and audit management. The smooth execution of these activities improves the transparency of safety concerns in the workplace. Further aids the generation of actionable insights on safety processes.
Mobile tools are increasingly being used to complete tasks and oversee the safety of employees who use mobile devices on the job. In particular, workplace safety tools (such as mobile inspection and incident applications) are expected to become more prevalent, as are apps that turn off workers’ mobile devices when they are completing essential tasks.
The use of personal protective equipment (PPE) and worksite clothing with sensors that monitor, collect, and record biometric, location, and movement data in real time is on the rise. This “smart” equipment collects the same data as wearable devices, including the user’s heart rate, calories burned, steps walked, and blood pressure. This equipment also tracks advanced metrics like the user’s blood alcohol content, blood oxygen levels, sweat levels, and vital signs. Some products may even detect changes in environmental conditions. Next-generation smart PPE is expected to monitor workers’ fatigue and alertness, which may help managers determine who needs a break and when.
Personal protective equipment (PPE) is a vital part of employee safety apparel. These protective articles serve as the first line of defense in the event of an incident. Innovations in wearable technologies and the miniaturization of sensors have allowed safety tech startups and scaleups to convert PPE into smart devices. These smart PPE are capable of monitoring the condition of both the employee and their surroundings. They are also equipped with a panic button that is manually or automatically triggered when a fall or accident is detected. Other innovations in wearables have led to the development of exoskeletons that assist workers in tasks like lifting, climbing, and prolonged standing. Apart from these industrial solutions some startups also focus on wearable solutions for office environments that monitor employees’ vital signs and keep track of their health. This workplace safety trend thus provides organizations with real-time health and safety information about employees working in various locations.
As green cleaning and waste management continues to evolve, technology and innovation are being developed and adopted to enable greater efficiency, effectiveness, and safety. Smart sensors and devices can monitor and control cleaning and waste management activities, providing real-time data and feedback. Robotics and automation can perform tasks with greater speed, accuracy, and consistency, reducing labor and resource requirements. Additionally, artificial intelligence and machine learning can analyze data to provide insights and recommendations for optimization. By leveraging the power of digitalization and data-driven decision making, these green technology and innovation can help transform cleaning and waste management practices into a competitive advantage.
While countless businesses understand that a computerized maintenance management system (CMMS) reduces expenditures and increases maintenance and plant efficiency, many organizations fail to recognize that a modern CMMS, paired with an optimized maintenance program, enhances their safety and significantly reduces their carbon footprint.
As businesses become more aware of the importance of sustainable practices, it’s time to start looking at CMMS as more than just a solution to maintenance issues. By adopting a sustainable approach to maintenance operations and utilizing a CMMS to support those efforts, businesses can reap the benefits of improved sustainability performance and an enhanced bottom line.
The integration of the internet of things (IoT) into industrial processes and systems enables real-time data collection on the performance and condition of industrial equipment. This data is leveraged and applied to advanced data processing algorithms to enable prior scheduling of maintenance, which reduces the risk of equipment failure and downtime. IIoT-sourced data also allows manufacturing businesses to analyze and identify asset anomalies to enable data-driven decision-making in maintenance. Moreover, it enables remote monitoring and diagnosis of problems in the equipment, reducing the need for on-site maintenance.
In the context of industrial maintenance, digital twin is leveraged to simulate and analyze the equipment or production line performance in real time. This improves the reliability, efficiency, and effectiveness of manufacturing operations. By analyzing the simulated data, it is possible to determine the optimal intervals for performing maintenance tasks, such as inspections, repairs, or replacements. This reduces intervention frequency, which saves time and money while also improving OEE. Further, digital factory twins aid virtual, interactive, and customized training for maintenance technicians. Such environments allow maintenance technicians to practice and learn new skills in a safe, simulated, yet real-world environment.
In the area of industrial equipment maintenance, 3D printing can provide obvious benefits if used to create spare parts. There are numerous cases where an equipment malfunction will occur unless a component is replaced. In such cases, additive manufacturing can rapidly produce the needed part. This expedites maintenance times and reduces inventory costs.
3D printing is also an obvious solution when parts that are discontinued (i.e. no longer produced and/or provided by the equipment manufacturer) are needed. Printing a discontinued part increases a machine’s longevity, while removing the need for a costly replacement due to the lack of a certain part. Despite the fact that a complete replacement cannot be avoided for a long time, additive manufacturing provides a temporary solution that saves dollars and alleviates disruption of operations.
Immersive reality technologies, such as virtual reality (VR) and augmented reality (AR), improve industrial maintenance in several ways. For example, these technologies create interactive training environments and help technicians troubleshoot problems more efficiently and accurately. In particular, AR superimposes instructions or diagrams onto the equipment, making it easier for technicians to follow procedures and locate components. Companies also create 3D models of equipment and facilities to visualize and optimize maintenance schedules and procedures. Moreover, remote assistance using AR and VR delivers on-demand expert guidance and support from a distance to the maintenance technicians. Despite the cost of immersive technologies, companies invest in these technologies to improve the performance of maintenance technicians and reduce the risk of accidents.
The high cost of predictive maintenance may make it unaffordable for small and medium-sized enterprises (SMEs). To maintain the quality and cost efficiency of maintenance operations, the services of companies are leveraged and maintenance-as-a-service (MaaS) is offered. SMEs also get the advantage of subscription models that balances the cost of maintenance. Moreover, maintenance equipment manufacturers benefit from additional business opportunities by ensuring recurring revenue. These services include software solutions such as computerized maintenance management systems (CMMS) and hardware solutions that include robots and other equipment like safety gear. Further, startups and scaleups provide services such as periodic calibration and lubrication services.
The use of robotics in maintenance operations offers benefits such as better efficiency, reduced costs, and improved safety. For instance, collaborative robots or cobots work alongside human technicians to perform maintenance tasks. Companies also leverage autonomous mobile robots (AMRs) that navigate through facilities and perform routine maintenance tasks like cleaning, inspection, and data collection, without human intervention. Additionally, there is a growing interest in the use of drones for maintenance inspections in hard-to-reach areas like oil rigs and manufacturing plants.
We now have increased access to low-cost, multi-purpose sensors and sensor networks, which can be attached to industrial equipment in several ways. As a result, modern plants often employ hundreds of sensors, which are used to collect maintenance data. At the same time, IoT enables the formation of smart networks for such sensors (including networks of wireless sensors), which facilitate the automated collection of sensor data.
Automated data collection negates the need for often costly, time-consuming and error-prone manual data collection processes. It also allows the preprocessing of data close to the source. This provides additional benefits through simplifying data cleaning and preparation processes. With this approach, IoT systems for data collection can seamlessly integrate with data analytics systems, saving additional effort and time.
Maintenance analytics is a rapidly advancing trend within industrial maintenance that employs advanced data analysis techniques to optimize equipment maintenance and minimize downtime. One prevailing trend in maintenance analytics is the integration of data from heterogeneous sources, such as sensors, equipment logs, and maintenance records, to obtain a more holistic view of equipment health and performance. Moreover, there is a growing interest in utilizing this data to provide remote assistance and training for maintenance technicians. Finally, cloud-based analytics platforms are gaining traction as they facilitate real-time monitoring and analysis of equipment performance data while also enabling informed decision-making.
Integrating big data and advanced analytics into asset data enables predictive maintenance for factories to forecast equipment conditions and failures. As part of proactive maintenance, sensors and cameras record large sets of data on temperature, vibrations, and conductivity, among others. Such solutions then transmit the data to software platforms to identify anomalies using AI and machine learning algorithms. Industrial asset management teams leverage this technology to estimate when maintenance should be performed, thereby allowing asset replacement or repair before failure.
An HMI is a user interface that allows operators to interact with and control industrial machinery and equipment. Factories and manufacturing plants implement HMIs through various methods, such as dedicated control panels, touchscreen displays, and mobile devices. They feature alarms, alerts, and data logging to help operators monitor and manage equipment performance. Through these features, HMIs improve the efficiency and effectiveness of industrial maintenance by providing real-time data and diagnostic information. Further, the integration of artificial intelligence (AI), machine learning (ML), and cloud-based HMIs provides operators with actionable insights and recommendations. This enables real-time collaboration, data sharing between multiple users, and remote maintenance.
Digitizing the industry is already having a tremendous impact on supply chain operations. It enables collecting digital information from multiple devices and across all phases of the supply chain.
Streamlining supply chain management information has proven to be extremely beneficial for industrial maintenance as well as it reduces the delivery times for parts. At the same time, supply chain operators benefit from maintenance insights, such as predictive maintenance. This helps ensure the timely placement of orders associated with the maintenance processes.